|
|
VirtualLab Fusion£ºHigh-NA Beam Splitter Optimization with UserDefined Merit Functions |
Time: 2022-12-17 21:06Source: infocrops.comWriter: infocrops |
Abstract
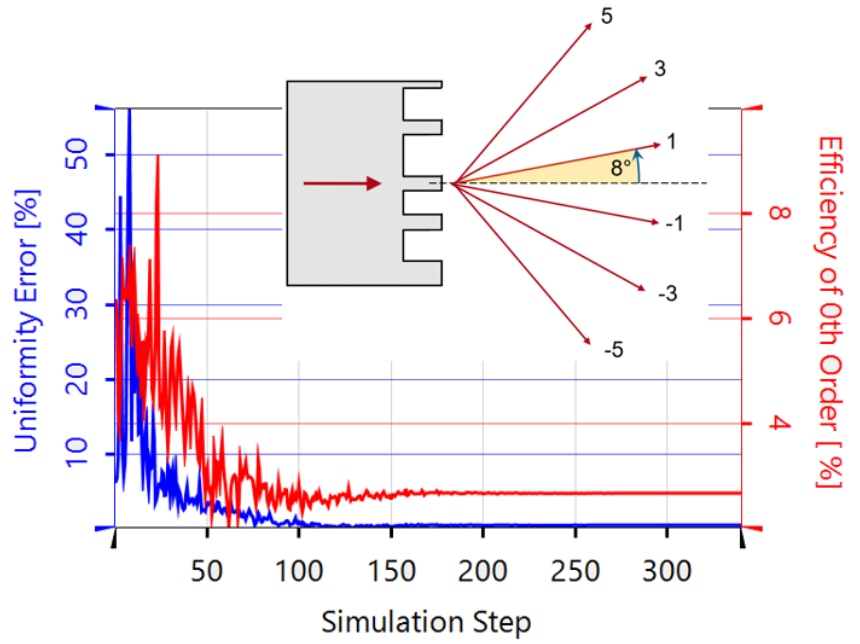
Diffractive beam splitters are often designed by applying certain paraxial approximations due to the direct relation between phase and structure and vice versa, which these algorithms provide. In case of non -paraxial or even high -NA splitters these approximations will introduce some inaccuracy and hence at least a rigorous analysis is advised, if not an additional rigorous post -optimization. In this use case, such rigorous evaluations are performed for an exemplary binary 1:6 splitter, using the odd diffraction orders. For this purpose, the structure of the initial system is parametrized, and a set of user -defined merit functions are defined via the Programmable Grating Analyzer. For the parametric optimization and subsequent tolerance analysis, the rigorous Fourier Modal Method (FMM) is used.
Modeling Task
How to optimize the surface profile of the following diffractive highNA 1:6 beam splitter to achieve optimal uniformity of the desired working orders?
light parameters
• wavelength: 632.63 nm
• polarization: along xdirection
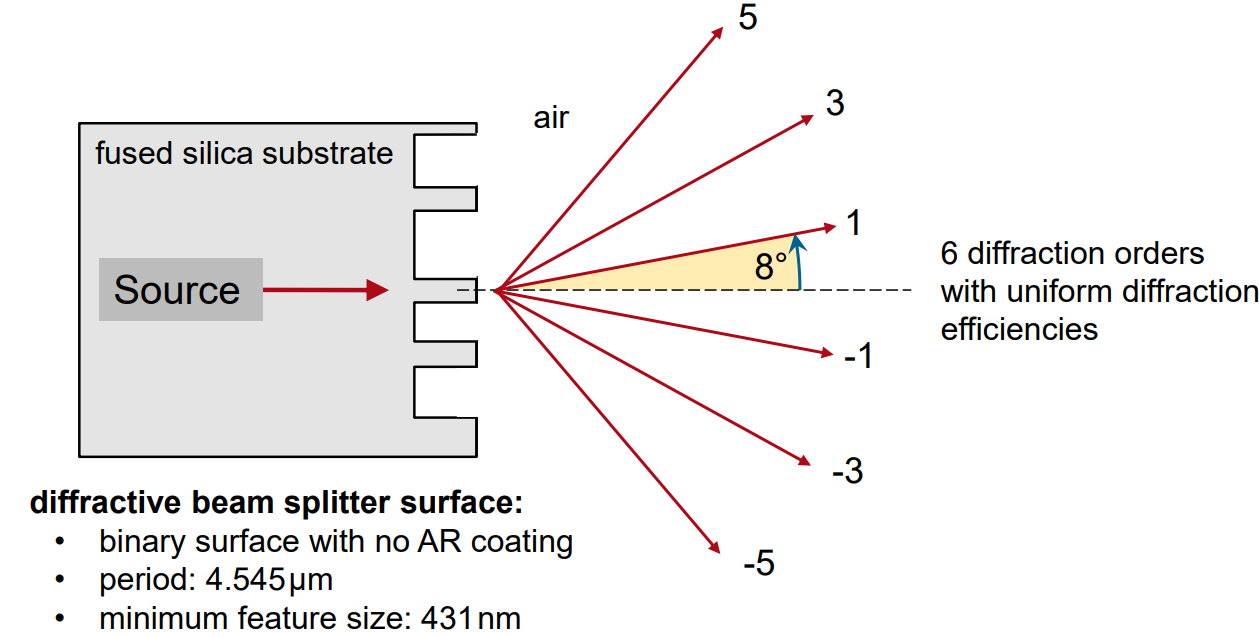
Initial Design of Diffractive Beam Splitter Surface
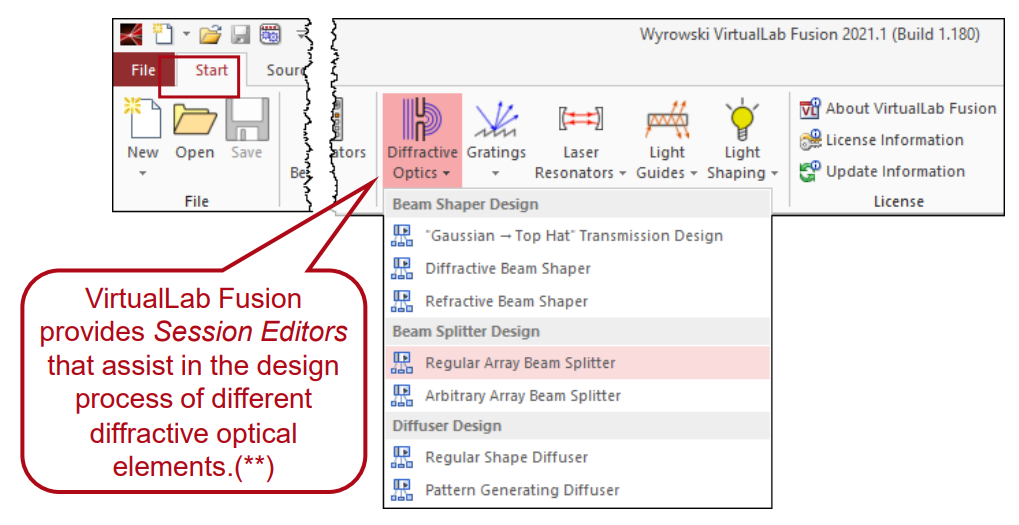
1. The initial beam splitter phase function was calculated by VirtualLab Fusion’s Iterative Fourier Transform Algorithm (IFTA) design tool.
2. For the conversion to a height profile, a structure design based on the Thin Element Approximation (TEA) was applied.
Limitations of TEA and an Equidistant Sampled Structure
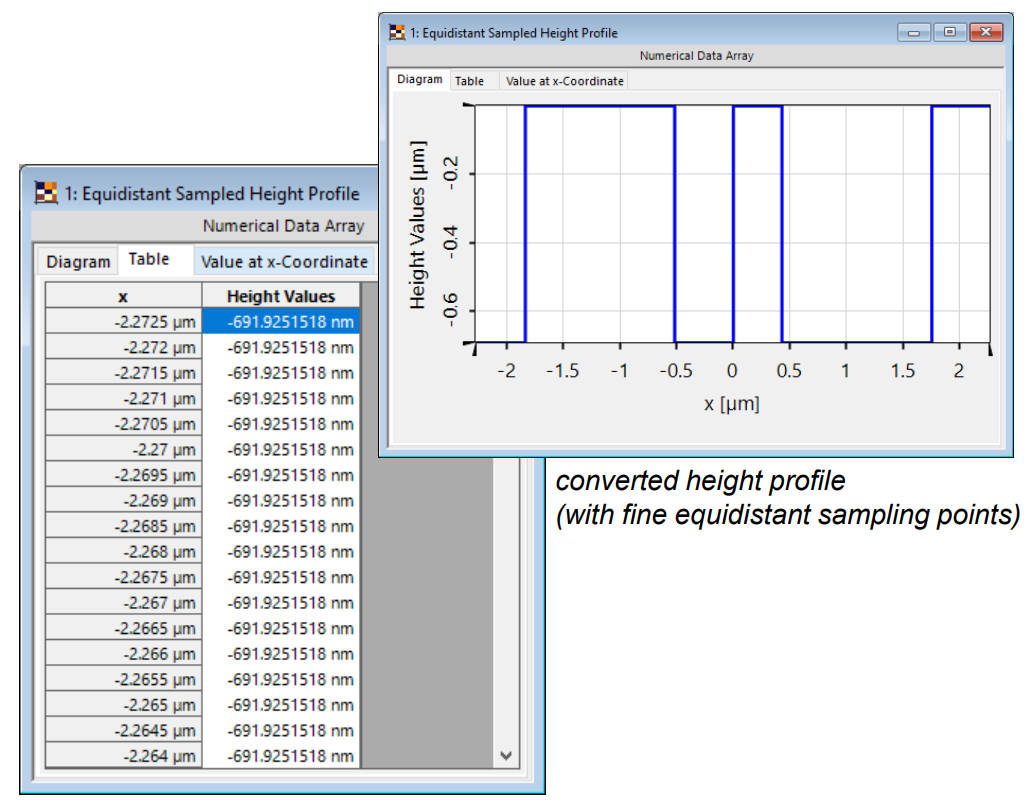
• TEA is well suited if the smallest feature sizes are not smaller than ~5 times the wavelength. If this is not the case, the amplitude/phase distribution after interacting with the designed height profile might exhibit relevant deviations from the desired values.
• Thus, a rigorous evaluation is needed.
• And for a parametric optimization, the structure data needs to be defined differently.
Data Preparation (Parametrization) for Post-Optimization
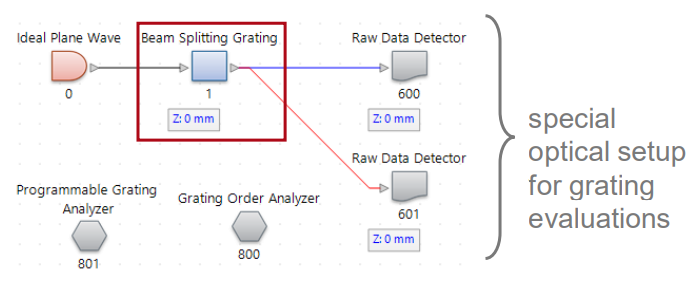
• For a rigorous analysis with the Fourier Modal Method (FMM), the sampled height profile from the structure design can directly be used.
• However, for a parametric optimization, the structure needs to be parametrized so that a suitable set of parameters can be used for the optimization.
• For this purpose, a VirtualLab Fusion module is used which converts the equidistantly sampled surface data into a non-equidistant transition point list (included in attached sample files).
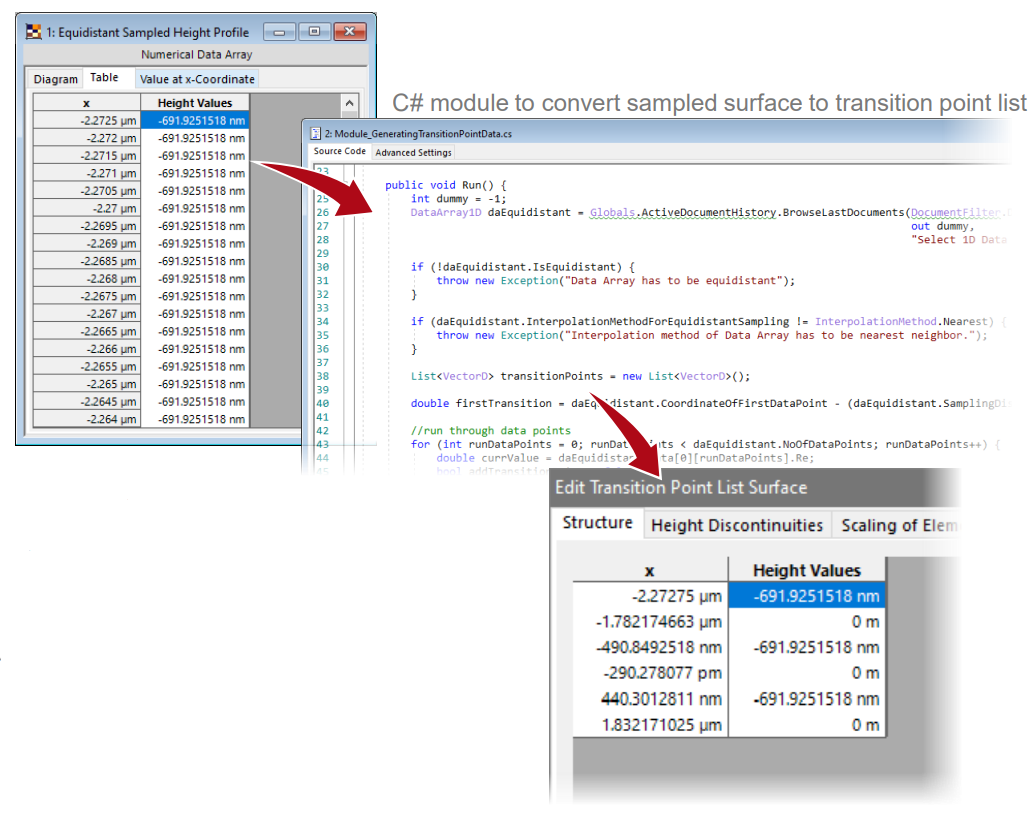
Diffractive Beam Splitter Surface for Further Optimization

Which Merit Functions for Which Diffraction Orders?
For the optimization it is not just relevant to have a wellparametrized structure, it is also important to define suitable merit functions, which are calculated based on distinct diffraction order results. In this use case the following merit functions are defined: 1. Efficiency of Desired (Working) Orders 2. Uniformity Error of Desired (Working) Orders 3. Maximum Efficiency of Undesired Orders (excl. 0th) 4. Efficiency of Undesired 0th Order 5. Efficiency of Undesired Orders The six desired (working) orders are: -5, -3, -1, 1, 3, 5 How many undesired orders are to be considered? → We used VirtualLab Fusion's Diffraction Angle Calculator to ascertain the number of propagating orders.
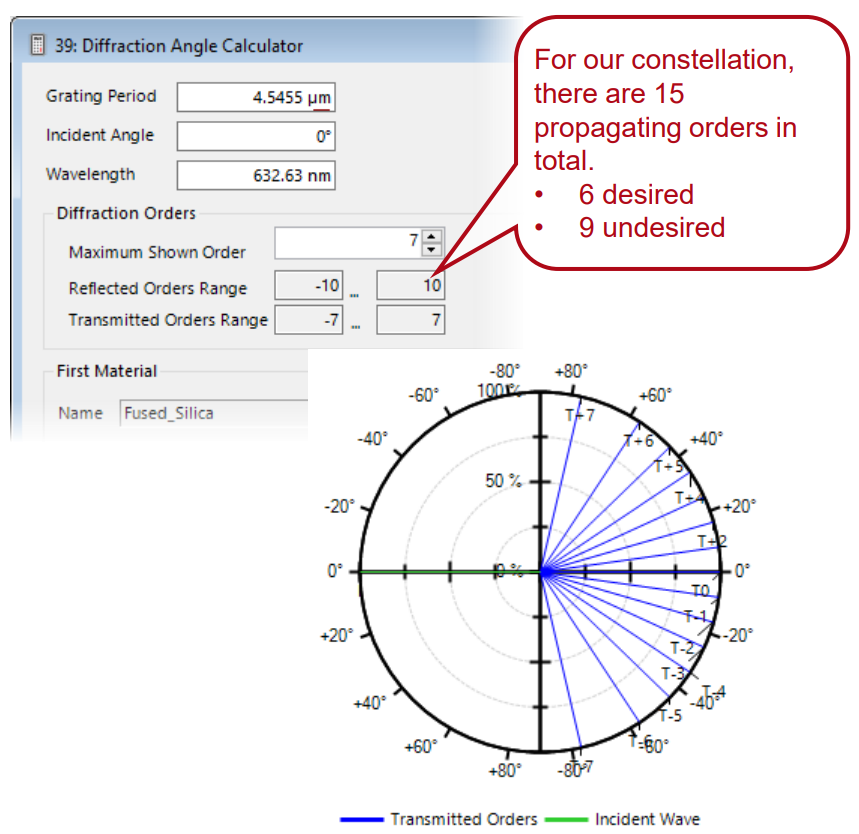
Using the Programmable Grating Analyzer
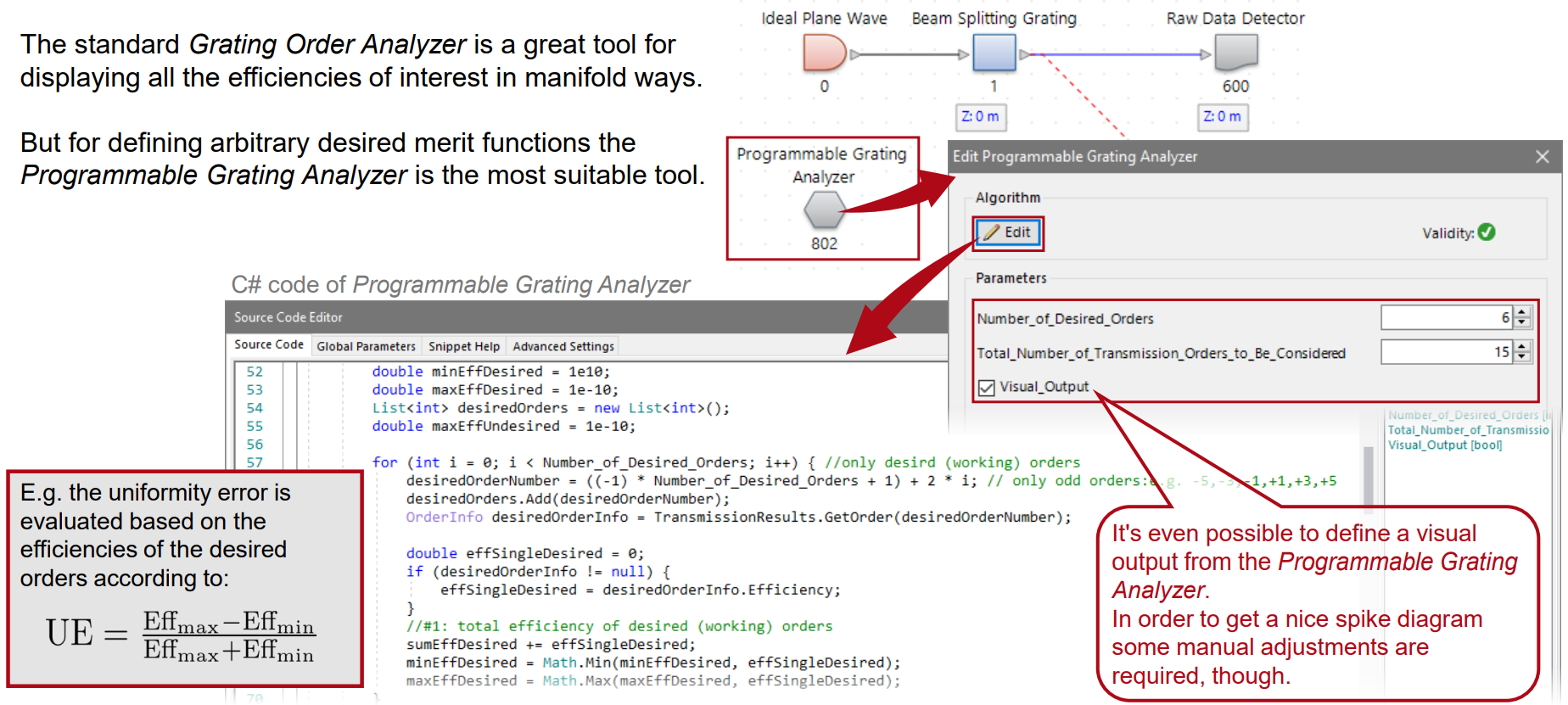
Rigorous Analysis of Initial Beamsplitter Design
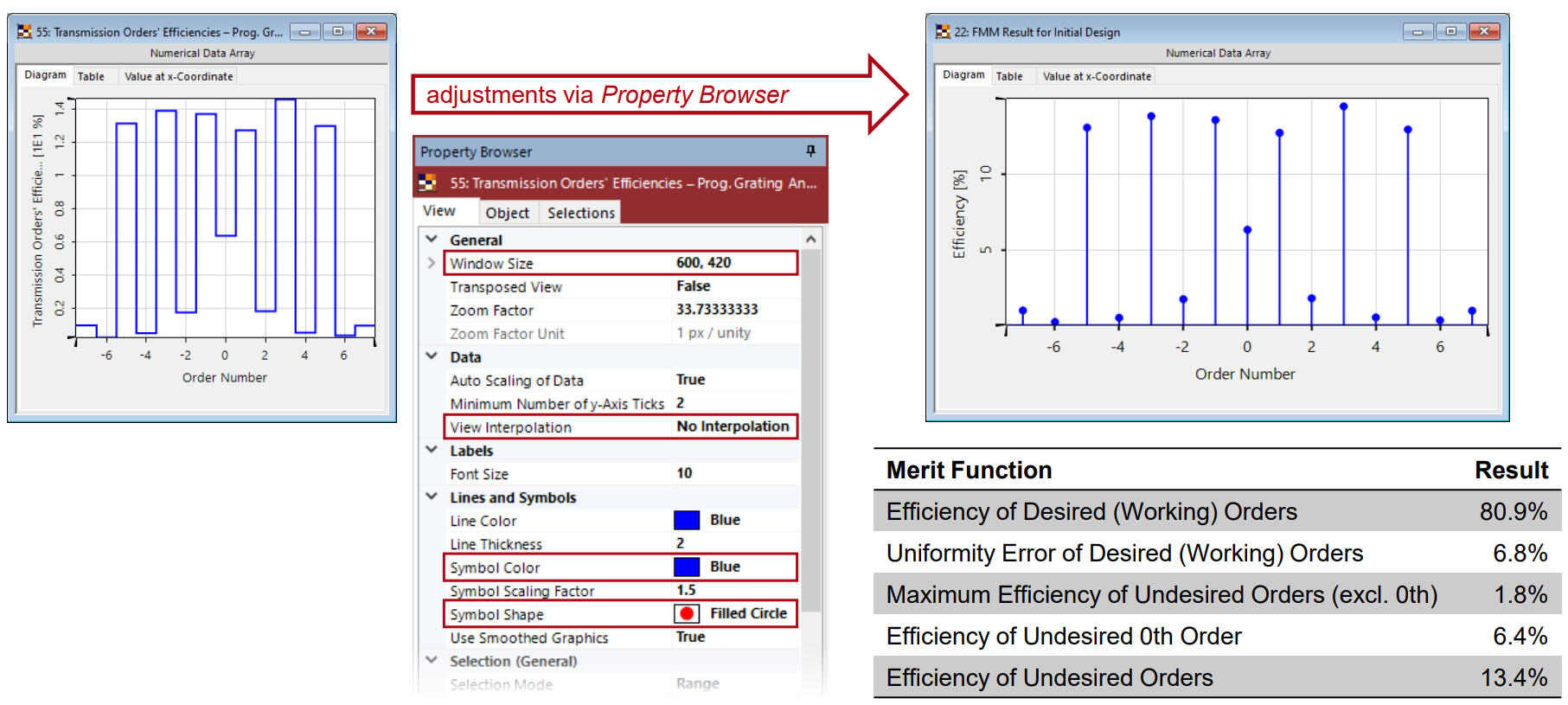
Set the Optimization Parameters
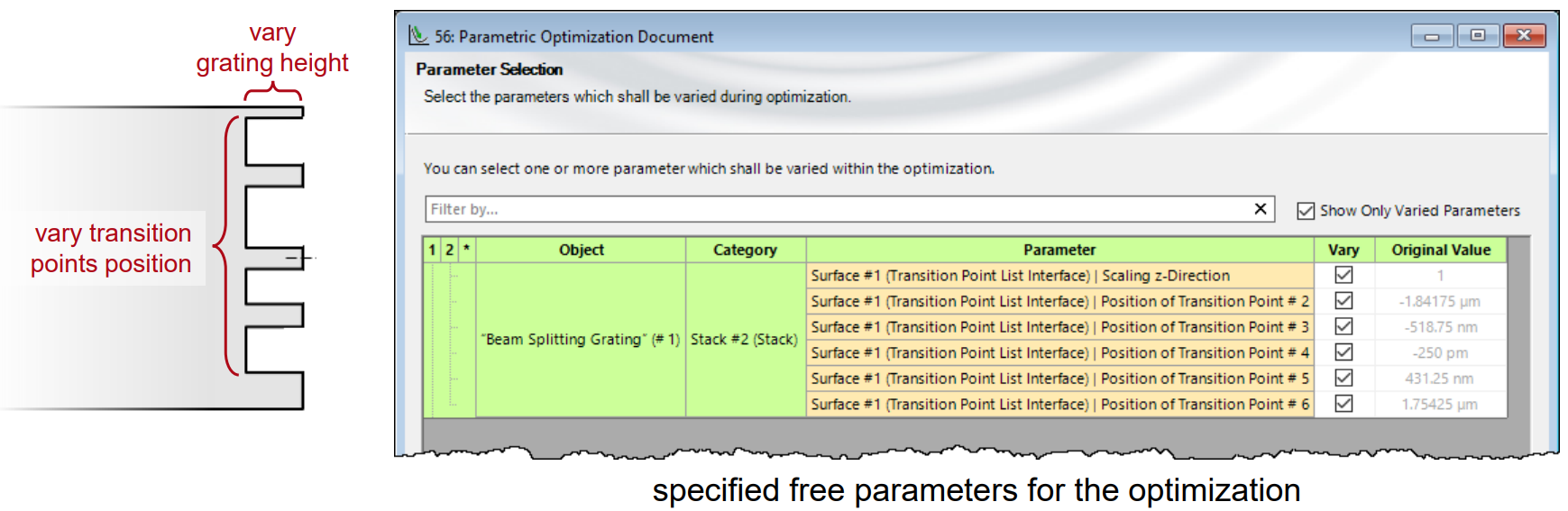
Two Optimization Processes for Comparison
In this use case we demonstrate two optimizations with differently configured aims and constraints:
• In optimization #1, the uniformity error is prioritized.
• In optimization #2, the 0th order should be minimized as well.
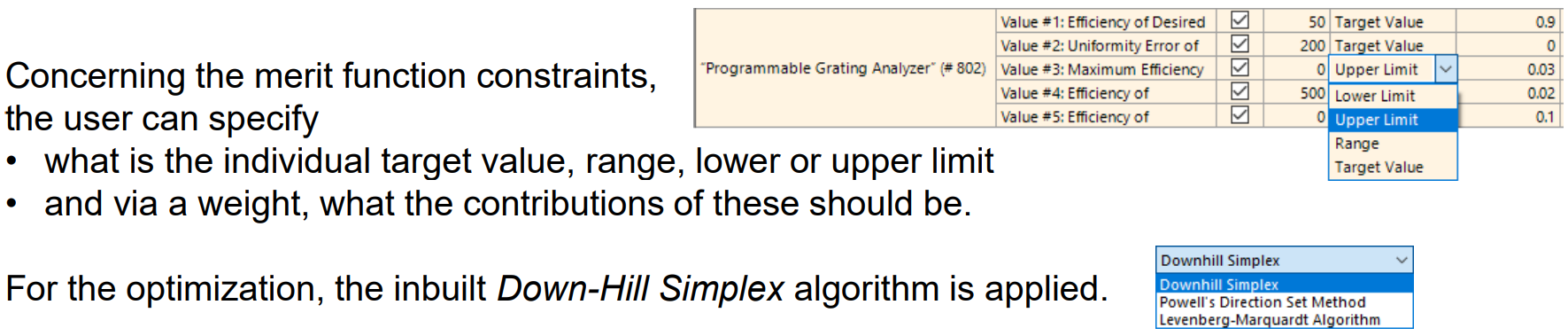
Configuration of the Merit Function Constraints
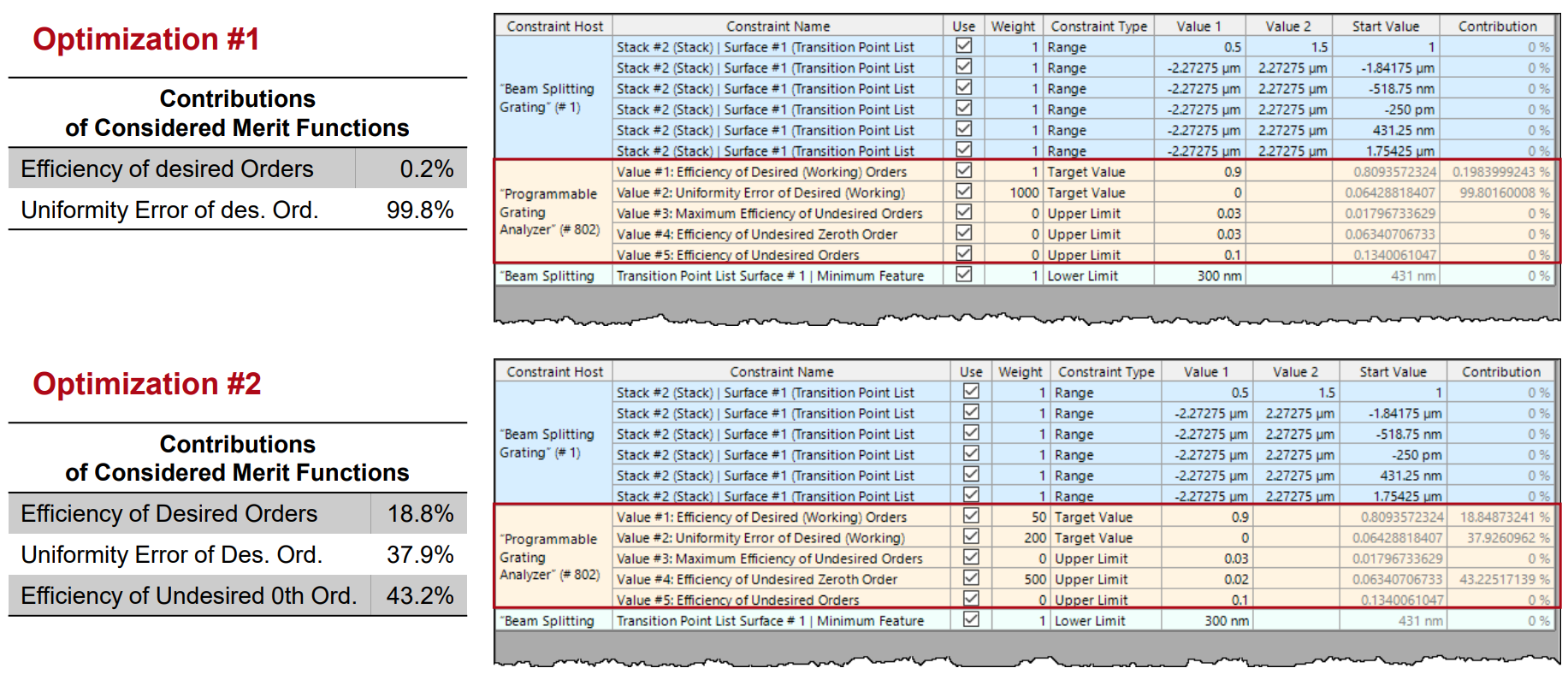
Optimization #1 (Priority = Uniformity Error)
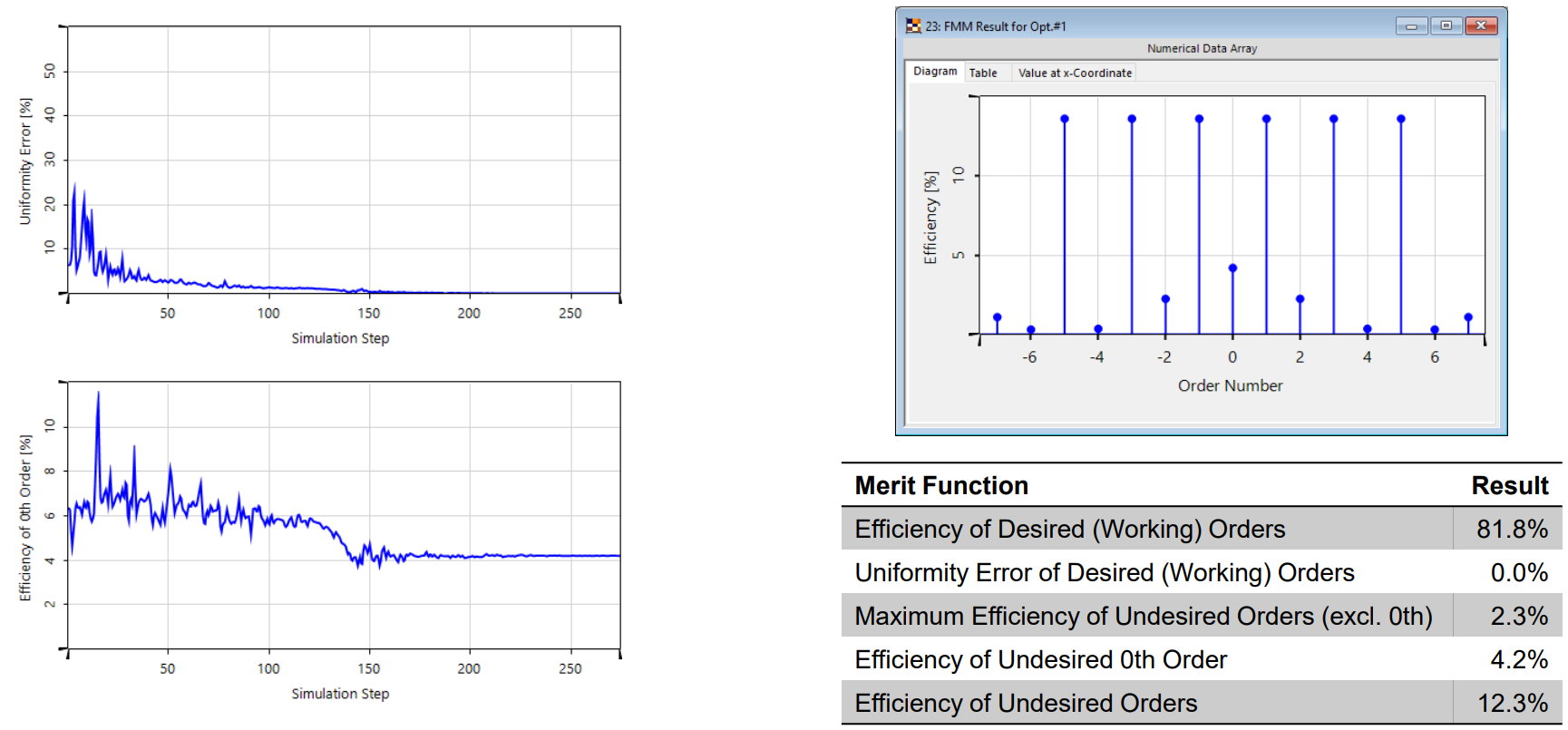
Optimization #2 (Priority = Uniformity Error & Low 0th Order)
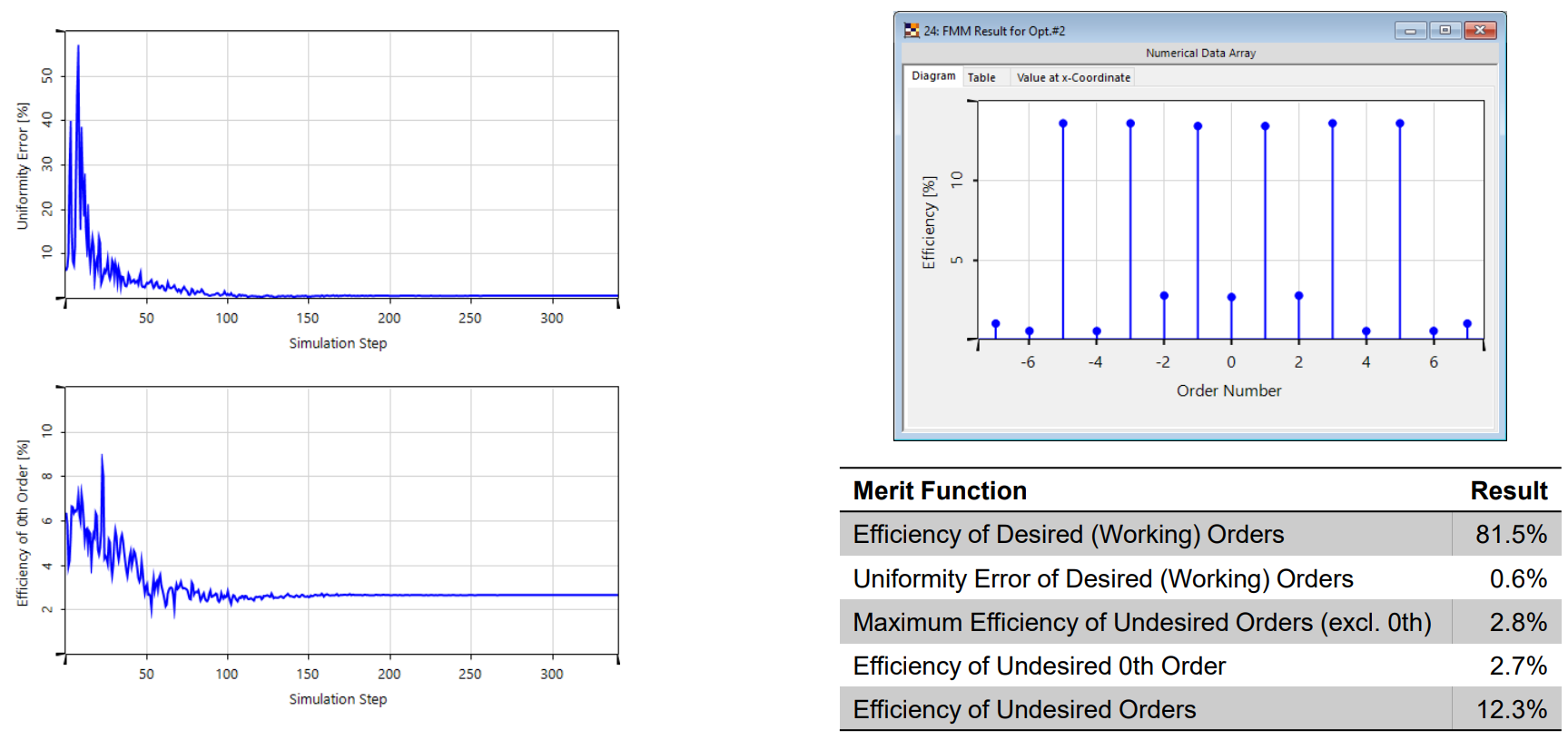
Comparison of Rigorous Results (Initial – Opt.#1 – Opt.#2)
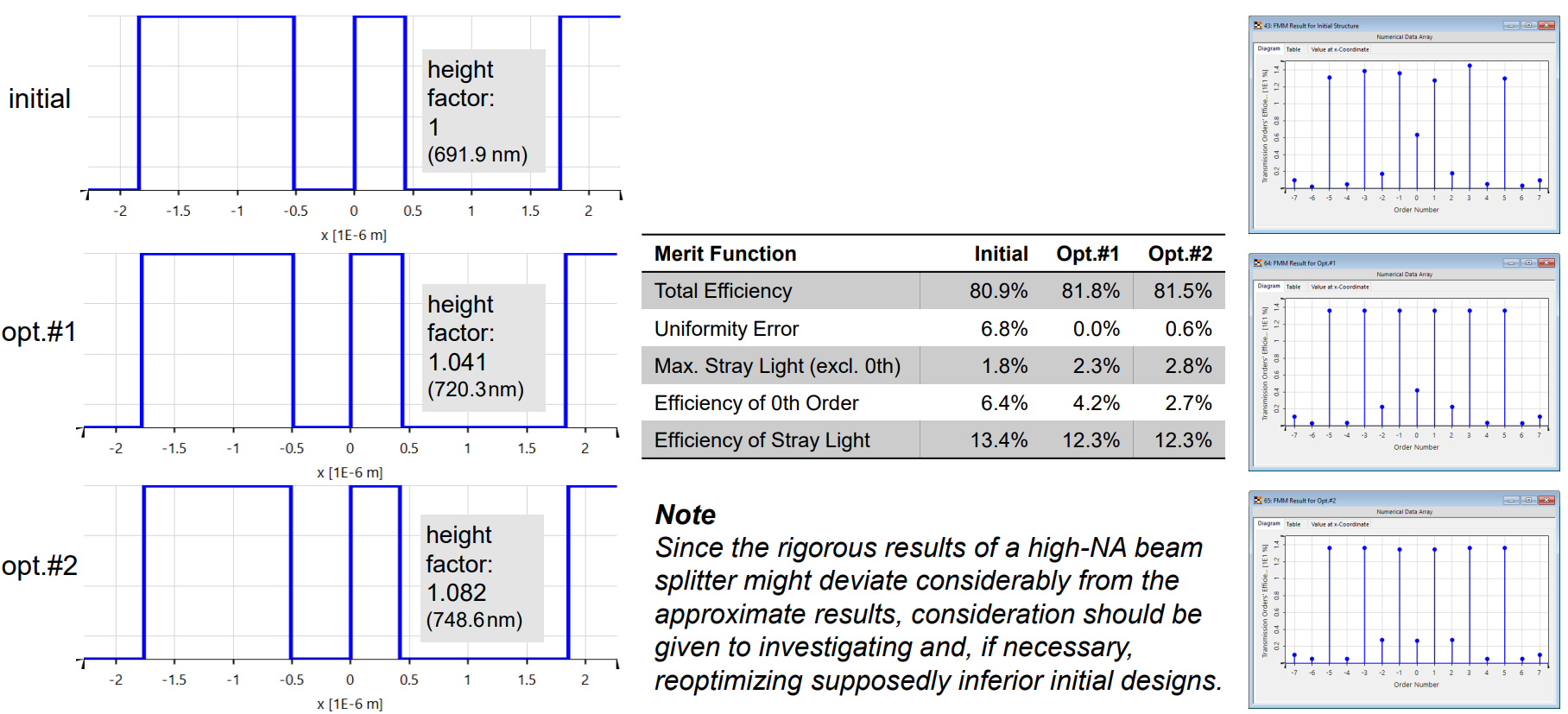
Results from Tolerance Simulations
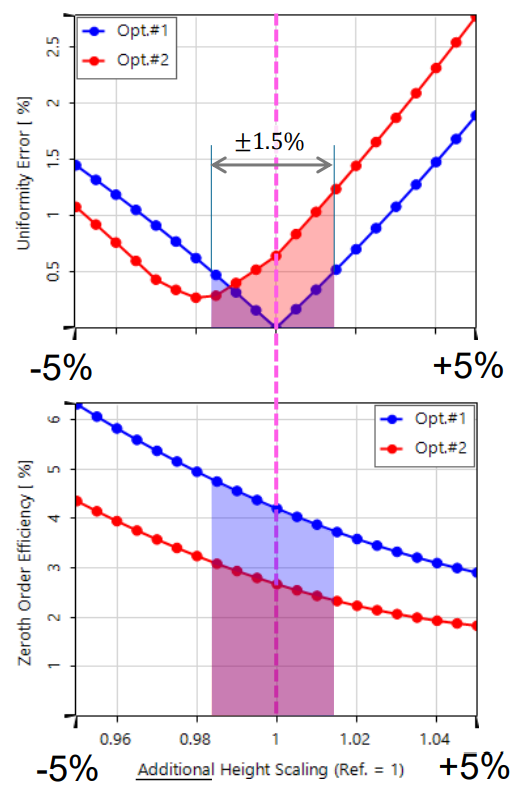
• It was investigated how the quality functions behave for possibly height tolerances during production in the range of ±5%.
• In most parts of the tolerancing range regarding an etching depth error of approx. ±1.5% (length of blue & red areas), the design from the 2nd optimization exhibits a distinctly worse uniformity.
• At first glance, it may seem strange for optimization #2 the minimal uniformity error (red curve @0%) is not centered. This is because low 0th order efficiency was prioritized in optimization #2 and some uniformity was sacrificed to achieve this aim.
• As a result, the structure of the 2 nd optimization has always a distinct lower 0th order for the whole envisaged range of the tolerancing analysis.
Note: The reference value 1 in the tolerance simulation results always refers to the individually optimized height of the examined structure (indicated by the purple line).
Conclusion from Tolerance Simulations
• Tolerance testing provides a better information base for deciding what is the most suitable structure for the desired application.
• It can be seen, that the structure of the 2nd optimization yields uniformity errors below 0.5% (green line) over a similar tolerancing range of ±1.3% (length of yellow area) if the height with the lowest uniformity error is used.
• Thus, the 2nd optimization result with an additional height scaling of 0.9825 (707.7 nm) might pose a good solution with an overall suitable performance. In below table the according results are shown in the last column titled "Opt.#2b".
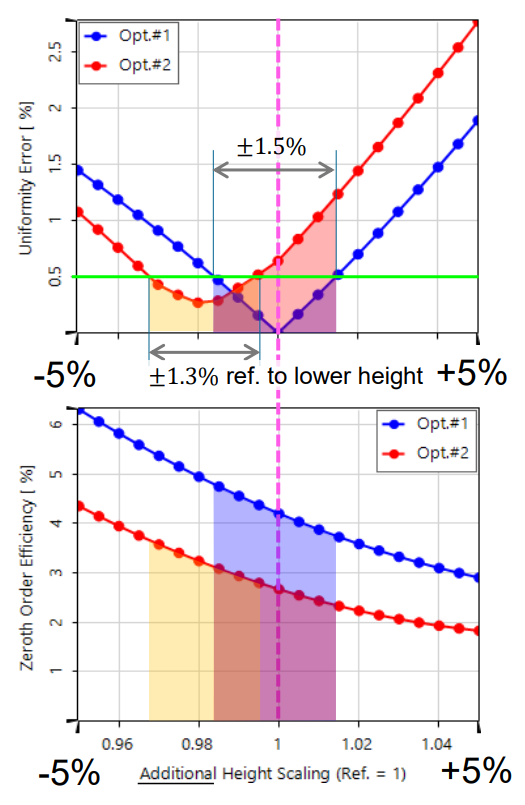
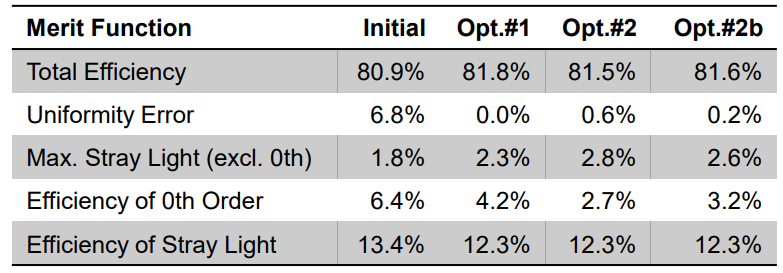
Document Information
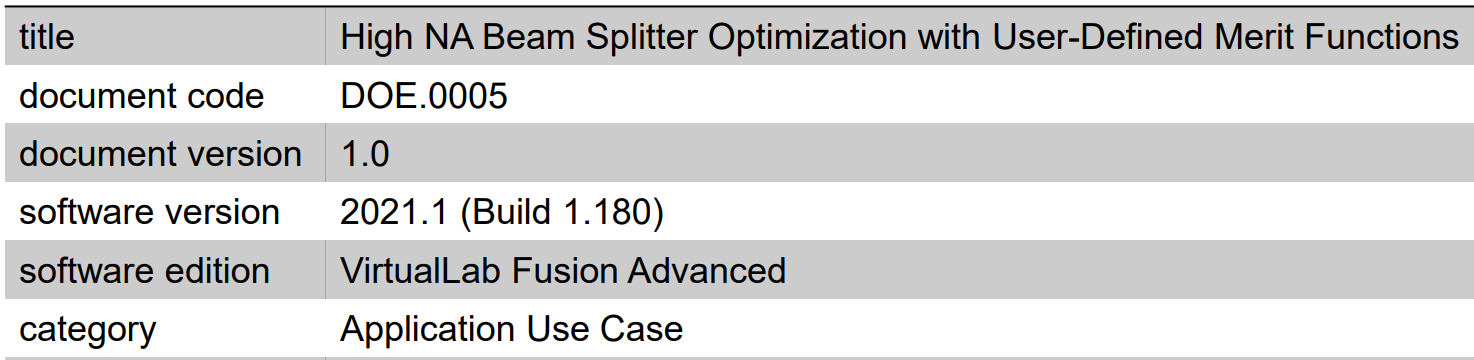
further reading
- Programmable Grating Analyzer
- Design and Rigorous Analysis of Non-Paraxial Diffractive Beam Splitter
- Design of Diffractive Beam Splitters for Generating a 2D Light Mark |
|
|
|